Background
Following a long-standing working association between the Zephyr's owners and D H Marine (Shetland) Ltd. spanning 18 years (the Zephyr is the 5th vessel of the same name to be owned by the Irvine family), the team got together in 2015 to start on the design process for the new boat which was delivered in 2019.
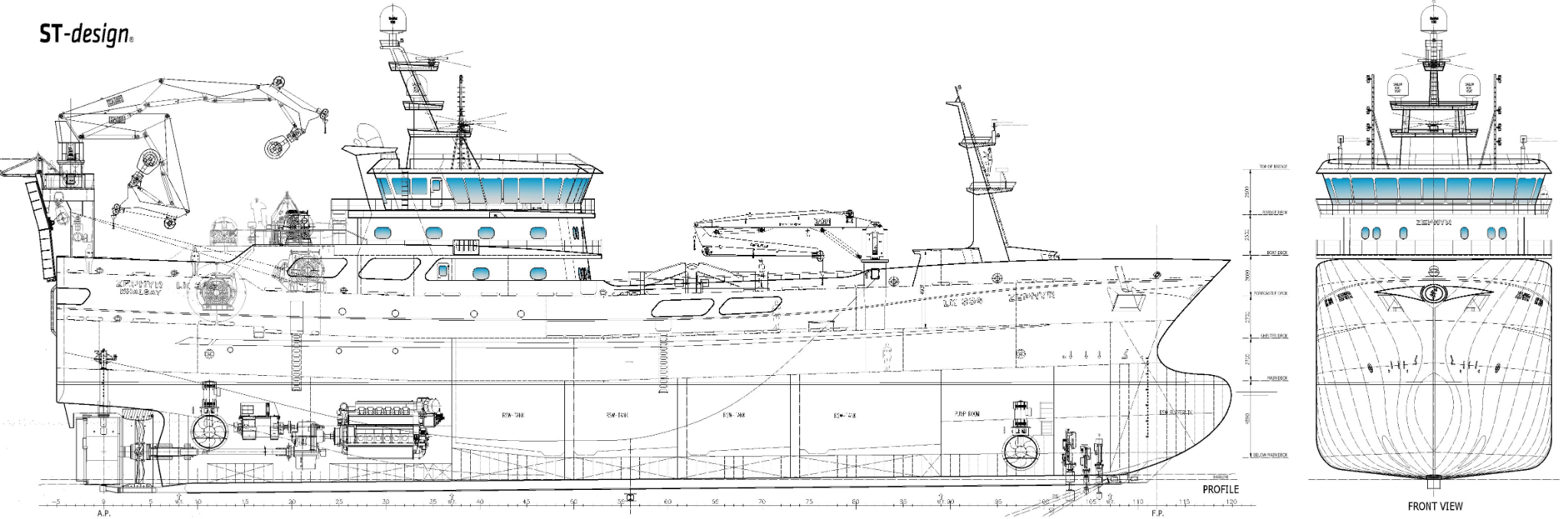
Particular emphasis was placed on the choice of engine room machinery, together with the integration of power generation and vessel control system. Utilising the knowledge and expertise of D H Marine, six Caterpillar auxiliary generators were specified as part of a customised and fully integrated electrical power supply system. This is a significant first for a pelagic vessel and will provide the best possible levels of operating efficiency for the Zephyr's owners.
Power Generation
A Wärtsilä 6960kW engine drives a 4m diameter 4 bladed propeller through a Wärtsilä SVC95 5.22:1 reduction gearbox. A power take off shaft on the gear box drives a Wärtsilä 3.1MW generator that provides electrical power to the electro-hydraulic motors.
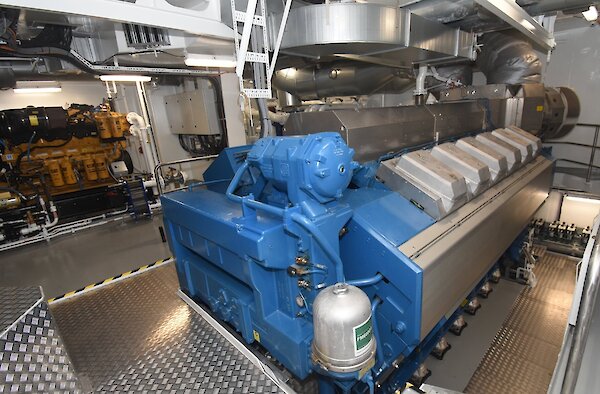
The six Caterpillar auxiliary generators are tasked to run a predetermined range of machinery:
- Caterpillar C32 models developing 940kW- these are the two largest generators and are designed to power the ships two refrigerated sea water systems when operating with full fish tanks.
- When the Zephyr is landing, a Caterpillar C18 generator provides 565kW of power to run the associated equipment
- A Caterpillar C9 generator delivers 300kW to run the vessel and power the cranes and mooring winches when in harbour
- When berthed and no shore power is available, a Caterpillar C7.1 developing 175kW will run continuously to heat both the vessel and the main engine. A second C7.1 unit delivering 138kW is used for emergency backup in a black ship situation and can also act as a second harbour set, back feeding an emergency switchboard to run the vessel whilst berthed for long periods.
The combined electrical power produced by the four Caterpillar generators totals an impressive 2.7MW and can be used to power the ship when the shaft driven generator is out of service.
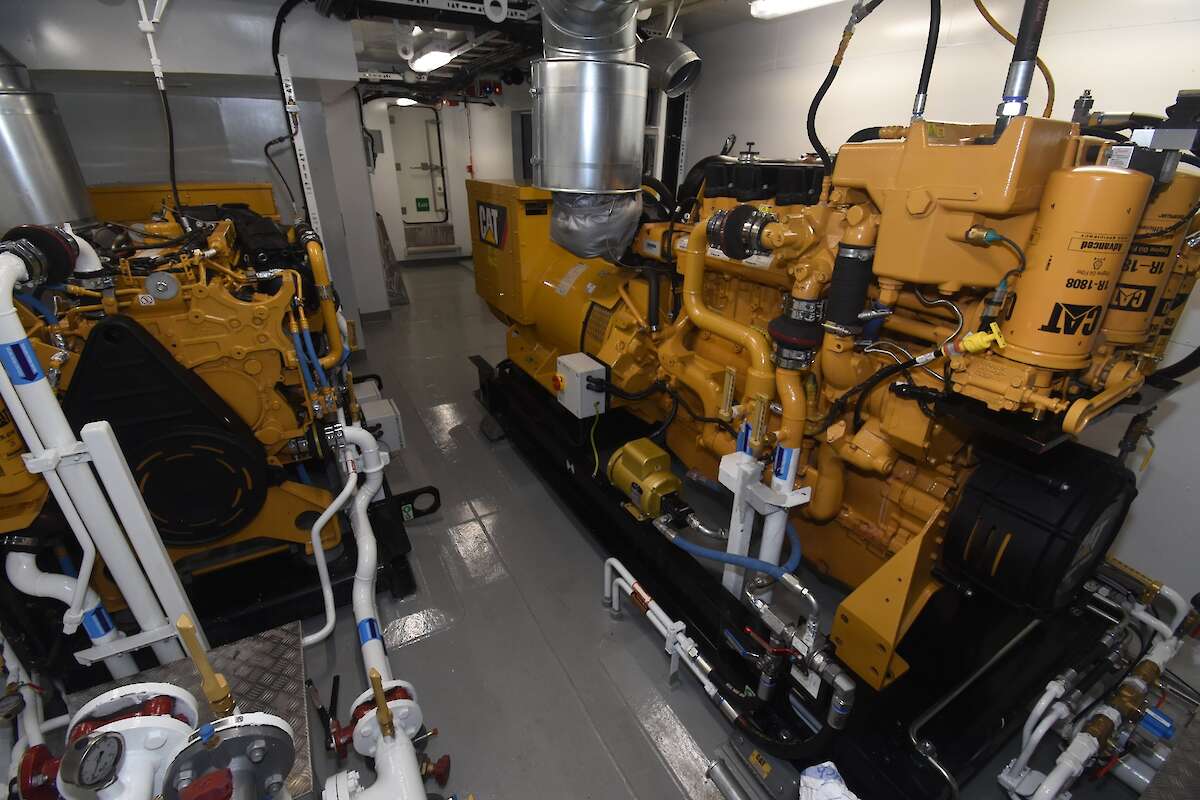
Power Generation Control
Matching the numerous electrical demands of the vessel with the various electrical power supplies is key to maximising efficiencies. In partnership with BlueDay Technology, D H Marine produced a custom designed Power Management System (PMS) that moderates the available power to match the call from the many motors, drives, pumps and heaters on board to minimise fuel consumption, reduce greenhouse emissions and maximise service intervals.
The system is monitored and operated through control screens that are located in the wheelhouse, engine room and main switchboard, with duplicate screens also installed in front of each control cabinet.
A separate customised Integrated Alarm System (IAS) was also developed, which keeps a watching brief over all of the critical plant and equipment. Operating as a stand alone system it constantly monitors sensors throughout the ship and will raise alerts at pre-determined levels to help safeguard the vessel and her crew.
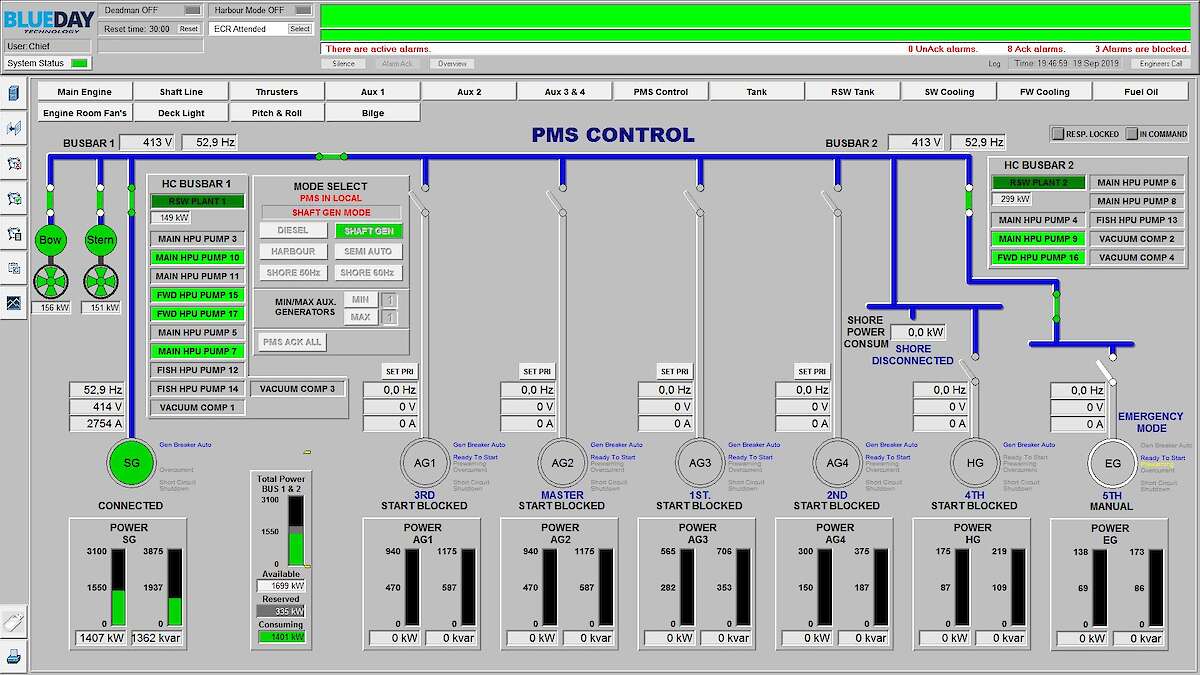
Heat Recovery
Heat produced by the C7 generator is used by two separate systems, a high temperature (HT) side and a low temperature (LT) side.
The HT side heats the main engine via a closed loop water system teed into the coolant jacket and keeps it at a steady 62°C for optimum starting conditions and rapid 'on-load' performance.
The LT side is integrated into the vessel's domestic hot water system, which provides warm water for the hotel services and for the Aeron air-conditioning units that blow warm air throughout the vessel to maintain a comfortable ambient temperature.
A bespoke calorifier provides an additional source of heat, with several immersion heater elements able to be switched on to match demand as required.
Hydraulics
Fish are pumped aboard using a hydraulically driven SeaQuest pump, which is lifted into the sea by the dedicated gantry mounted 4T crane.
Using the knowledge and support of our hose and coupling partner Hydroscand, D H Marine supplied and installed the 80m length of hydraulic hose (Hydroscand 2" DeltaFlex) that accompanies the pump as it descends into the catch.
A hose making machine together with a stock of Hydroscand hoses and couplings has been installed in the hydraulic room. This enables the engineers to make up hoses in an emergency should the need arise.
Keeping it Clean
To help keep the ship in pristine condition, D H Marine specified, supplied and installed a Nilfisk SC Delta high pressure washing system. The SC Delta is a multi pump, multi pressure system that supplies a series of jet lances via hose storage reels positioned throughout the ship.
The Final Result
At a time when a continual succession of midwater vessels are entering service in the Norwegian fleet, it is important that Scottish vessels are able to compete on an equal footing.
Skipper Allister Irvine said:
"While the boat represents a considerable learning curve for us initially in terms of the new technologies, as well as pumping aft, it is one we are looking forward to.
We are delighted with the end result, as there is no doubt that the yard, together with all the other companies involved, pulled out the stops to deliver a splendid boat, both in terms of working efficiency and finish."
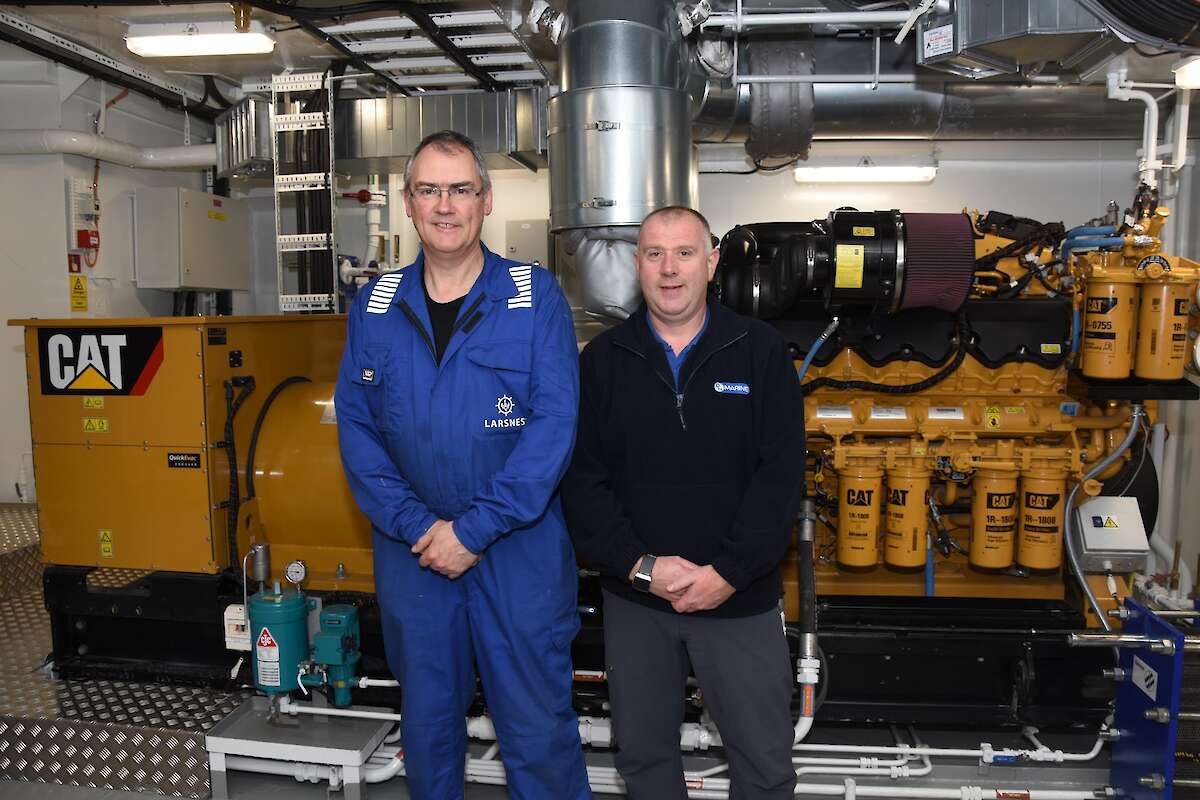
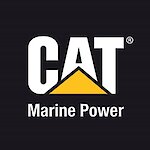
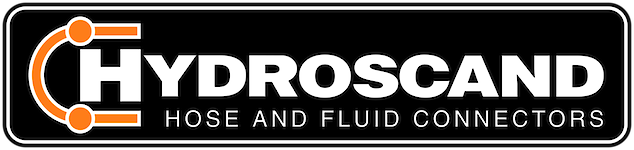

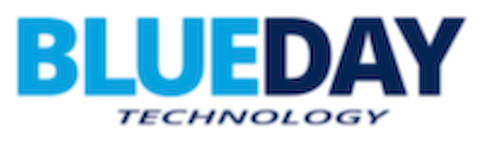